3D-Printed Shelby Cobra Debuts At 2015 Detroit Auto Show: From Concept To Reality In Just Six Weeks

The Department of Energy’s Oak Ridge National Laboratory (ORNL) debuted a fully functional 3D-printed Shelby Cobra at the 2015 North American International Auto Show in Detroit Monday. The car, honoring the 50th anniversary of the Shelby Cobra 289 FIA, weighs 1,400 pounds; 500 pounds of parts used on the vehicle were printed in just 24 hours. From concept to completion, it took six weeks to build.
The laboratory team did have the advantage of using the Big Area Additive Manufacturing (BAAM) machine, which can print parts 500 to 1,000 times faster than other industrial 3D printers. The BAAM machine received an upgrade after it was used to create the world's first 3D-printed car in 2014. The "Strati" was designed by Local Motors and developed by ORNL, Motor Trend reported. It contained just 40 parts and took 44 hours to print.
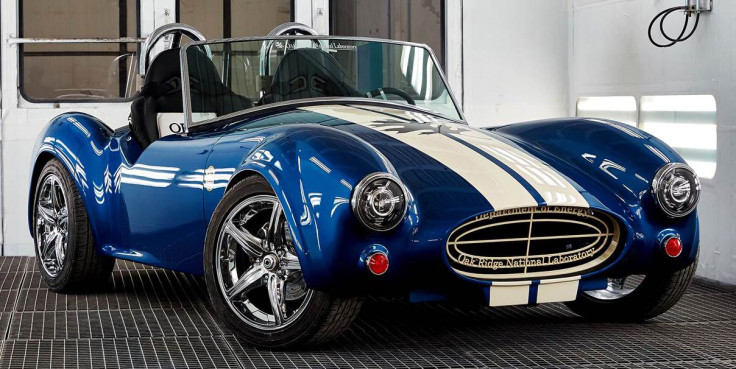
"You can print out a working vehicle in a matter of days or weeks," Lonnie Love, leader of ORNL’s Manufacturing Systems Research group, said in a statement. "You can test it for form, fit and function. Your ability to innovate quickly has radically changed. There’s a whole industry that could be built up around rapid innovation in transportation."
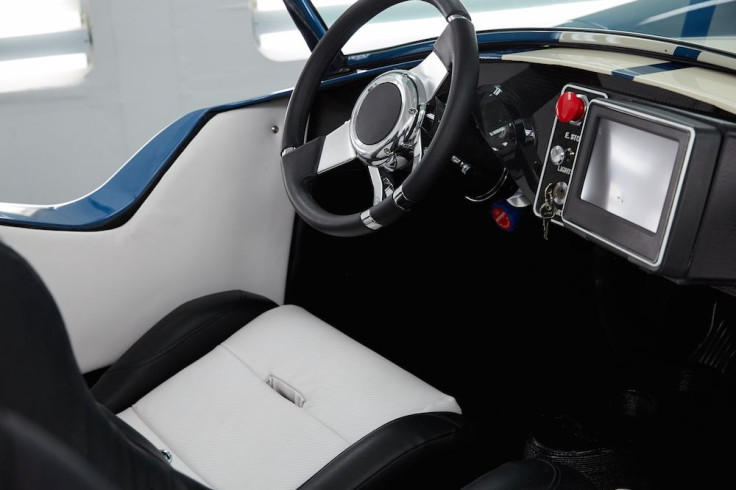
Printing components can greatly reduce the cost of developing prototype vehicles. The Cobra can be used to test new concepts and components, with the lab team easily able to swap out batteries, fuel cells, wireless charging systems and electronics. "Our goal is to demonstrate the potential of large-scale additive manufacturing as an innovative and viable manufacturing technology," Love said.
© Copyright IBTimes 2024. All rights reserved.