3D Printing With Metal: Engineers Create DIY Welding 3D Printer For Under $1,500
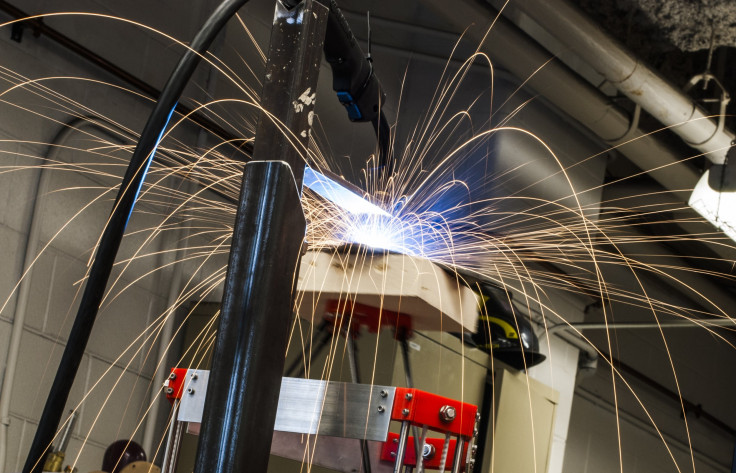
Currently, the commercial 3D printing landscape is dominated by contraptions that create everything from toys to watchbands out of plastic. But there’s another manufacturing revolution in the making: metal 3D printing.
Big companies like Rolls-Royce and GE are already working on using 3D printing to make metal parts for jet engines, but their machines have a startup cost of hundreds of thousands of dollars – not exactly within reach for the garage hobbyist. Now, engineers from Michigan Technological University in Houghton have rigged up their version of a 3D metal printer that can be made with less than $1,500 of materials and some open-source software. They outline their process – and include plans and a shopping list – in a paper appearing in the journal IEEE Access.
The primary ingredient in the metal printer is a small commercial MIG welder, which uses a special wire to maintain an electric current that heats metals and joins them together. The team also used an open-source 3D printer schematic derived from the plastic RepRap printer.
“Anyone that has more or less any kind of welding system can build our version of a 3D printer and get off to the races,” MTU engineer Joshua Pearce said in a phone interview.
Their metal printer creates objects from layers of steel wire, heated and extruded through a nozzle.
“We can [make] any 3D object that could fit in a breadbox,” Pearce says – with the caveat that the object cannot have any vertical holes running through it, because of how the welding machine works.
This isn’t the first venture to meld metal and 3D printing. Another 3D printer, the Mini Metal Maker, can be used to make small custom metal pieces, like jewelry, and will set you back just $750 (unassembled) or $1,000 (assembled). Instead of wire, this model prints with a blend of metal and clay. The piece is fired in a kiln afterwards, removing binders and water, and leaving behind the metal. Mini Metal Maker has raised more than $21,000 so far on the crowdfunding website Indiegogo, and expects to start shipping printer kits to backers in September 2014.
In contrast, the do-it-yourself model that Pearce and colleagues have put together is more suited to making machine parts for a metal shop or a garage – some place with extensive fire protection equipment and safety gear. This 3D metal printer prototype isn’t something you want to have in the living room.
Pearce and his colleagues printed out a sprocket and other parts with their prototype, and are already thinking about how to improve the next version of the printer. They’re also testing out other kinds of metals besides steel. The only real limit with this model, besides imagination, is the thickness of the welding wire, which determines the minimum resolution of the object that the printer can make.
Given that people have already been able to create plastic guns with 3D printers, the advent of metal 3D printers will surely make it easier for people to fabricate guns and knives at home. But is that a good enough reason to stifle the development of metal 3D printing?
“I’ve thought a lot about this, and I’ve come to these conclusions: All technology can be used for good and bad things,” Pearce says. “You can absolutely use this to make any manner of weapon, but the potential good implications annihilate the bad ones.”
In the developing world, having access to custom metal fabrication could be transformative. People could get parts for pumps, or windmills, or other essential machines, without having to pay the premium in money and time while waiting for replacement parts to be shipped out. People could print out the sprockets, gears and other parts of a bicycle, and use local materials like bamboo to create the frame.
Pearce says he’s also excited about the potential that 3D metal printing affords for scientific research. If scientists have access to cheaper and more customizable tools, research can progress even faster.
“What that’ll do is accelerate everything,” he says.
SOURCE: Anzalone et al. “A Low-Cost Open-Source Metal 3-D Printer.” IEEE Access published 2 December 2013.
© Copyright IBTimes 2024. All rights reserved.