Fear Of Slowing Economic Growth In China Spreads To Prosperous Pearl River Delta Region
As giant manufacturing hubs in China grapple with a slowdown in orders, migrant workers are struggling to find jobs — and worries are deepening about growth in the world’s second-largest economy.
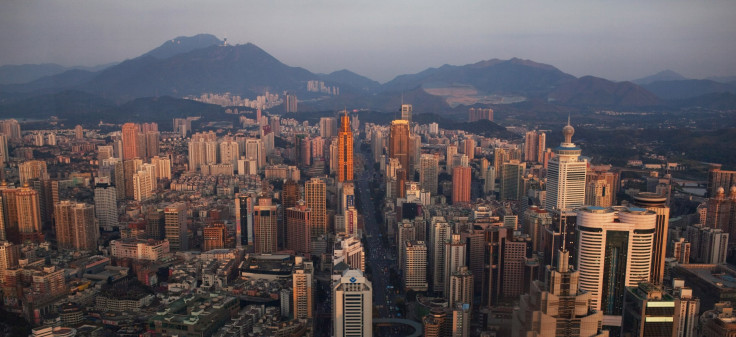
SHENZHEN, China — The last time this booming metropolis in southern China confronted the forces of an economic crisis — an international affair born in the United States that soon spread to Europe and Asia — the consequences barely registered on the factory floor. So powerful was the demand for Chinese-made goods worldwide that the legions of migrant workers streaming in from the countryside could reliably find a paycheck.
But this time, as China grapples with a mostly homegrown economic slowdown, the factories of the Pearl River Delta are hurting, with many suffering such a high rate of lost orders that they are laying off workers or even shutting down.
“It’s very strange,” says factory owner Grace Zhang, gazing around a minimalist café near her home in an upscale residential district of this city in Guangdong province, just across the border from Hong Kong. “In 2008-9, during the financial crisis, we had no problem — we didn’t feel much impact from the slowdown at all. And we were still doing fine last year. But this year it’s been slack all the time. There’s been a very serious shrinkage in our business, and it’s getting worse.”
Until recently, Zhang was a typical Shenzhen success story: an entrepreneur in this city in Guangdong province, one of the first to be designated a Special Economic Zone amid China’s early experiments with market reforms in the 1980s. She was representative of the glut of enterprising individuals who flocked to the city to “chase their dream,” as local government posters put it. She built her company into a thriving business, manufacturing luxury goods packaging, with a focus on jewelry. Zhang has enjoyed the fruits of her wealth, educating her children at private school, living in a spacious apartment and about to move into a bigger one.
But this year she’s had to lay off 50 percent of her staff, shrinking from 100 employees down to just 50.
“We start by cutting the temporary workers, and the ones who came more recently,” Zhang says. “We’re trying to keep the ones who’ve been with us longer. But it’s worrying. We’re so used to growing – from a small company to something much bigger.” She gives an ironic smile. “Maybe from next year we’ll start shrinking back from a big enterprise to a small one – and then one day not exist at all!”
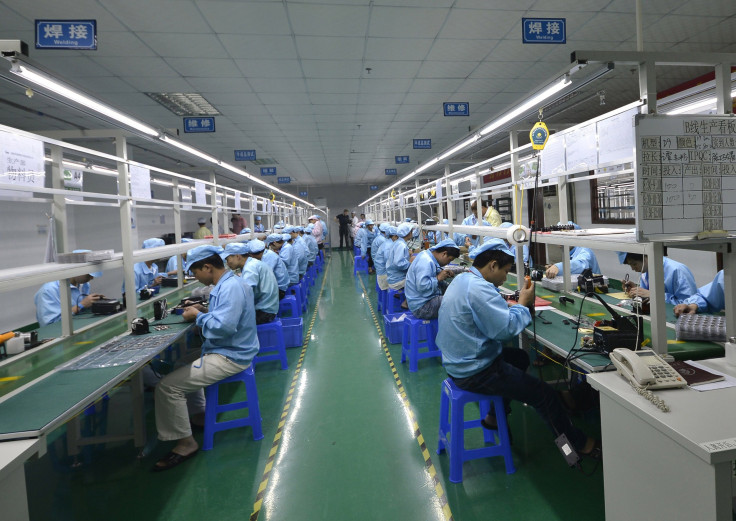
Zhang’s experience is far from isolated. Shenzhen, along with other parts of the Pearl River Delta — the heavily industrialized swath of Guangdong that alone generates some 10 percent of China’s wealth — has seen a number of unexpected factory closures in recent months, including companies in key growth industries, such as telecommunications.
The city's image for ever-more modern development has been further tarnished by the landslide at a rubbish dump in the city's industrial suburbs on Dec. 20, which destroyed more than 20 buildings at an industrial park, and left more than 80 people, including factory workers and their families, missing. Reports say safety officials had ordered the dump, which mainly contained earth and other construction waste, to close down, but the order was not enforced, despite repeated complaints from local residents.
In another sign of the strife that has replaced the boom in the Guangdong factory belt, strikes and labor disputes caused by plants shutting down or delaying payment of wages or welfare contributions have this year increased by some 40 percent, says Geoffrey Crothall, of Hong Kong-based monitoring group China Labor Bulletin. The vast majority of such episodes have occurred in the Pearl River Delta.
Guangdong Province, China

“Guangdong had 359 strikes in the first 11 months of this year,” Crothall says. “In November alone there were 56 — the highest monthly total we’ve seen since we began keeping records [almost five years ago]. There are factories closing every day.” The government has also detained some 20 labor activists in Guangdong in recent weeks, apparently in response to the growing number of strikes.
Zhang is concerned that her company might one day go the same way if orders, particularly from domestic clients, don’t pick up. While it’s the fall in China’s exports that has made headlines, pushing the nation’s GDP growth to its lowest level since the 2009 financial crisis, Zhang says demand from overseas customers – some 20 percent of her business — has held up; it’s domestic orders that have plunged in recent months. This may have been affected by China’s ongoing anti-corruption campaign, she acknowledges, or indeed a growing trend for wealthy Chinese shoppers to buy goods abroad, but she says it’s a sudden and unexpected development. And in a country where domestic demand is seen as a key economic driver as exports slow, it’s a worrying one, too. Recent data suggest that China’s domestic demand is starting to flag — and the global economy is likely to suffer the consequences, as Chinese demand for materials and other imported goods is reduced.
John Zhu, an analyst at HSBC in Hong Kong and the author of a recent research paper on China’s regions, says demand in China’s economy “isn’t at normal levels at the moment. It’s too low. Global demand has been very weak, but there’s also been a lack of domestic demand as well. It’s putting downward pressure on prices and profits, which is hitting some manufacturing sectors.” His view is borne out by the Purchasing Managers’ Index, measuring manufacturing activity and confidence, which has slumped into negative territory, and shows that factories are reducing staffing. At the same time, consumer confidence indexes, compiled by ANZ Bank and others, are also recording their lowest readings for many years, indicating challenges for one of the most important growth sectors of China’s economy.
Beyond the considerable economic scale of lower global — and domestic — demand, the troubles playing out in the Pearl River Delta raise nagging questions about the fitness of China’s mode of development in a time of grave uncertainty over future growth prospects. Shenzhen has long been championed by China’s ruling Communist Party as a showcase for the modernization of the national economy. Shenzhen has produced a crop of prominent, highly capitalized companies in technology, publishing and other advanced industries that are supposed to be able to weather the storm of a global slowdown. The region is at the forefront of China’s attempts to move up the value chain, and avoid getting caught in what economists call the “middle-income trap” — where rising labor costs drive low-end industry out of business, before a country has the research capacity and innovation base to move upstream into more-productive industries.
Shenzhen and other advanced areas of Guangdong province represent China’s effort to emulate the success of countries like South Korea and Singapore, which have evaded the trap, while avoiding the fate of South American countries like Brazil and Argentina, where rising wages delivered stagnation. Observers say a significant slowdown in Shenzhen would be a test for China’s ability to raise wages and could be damaging for China’s economy as a whole.
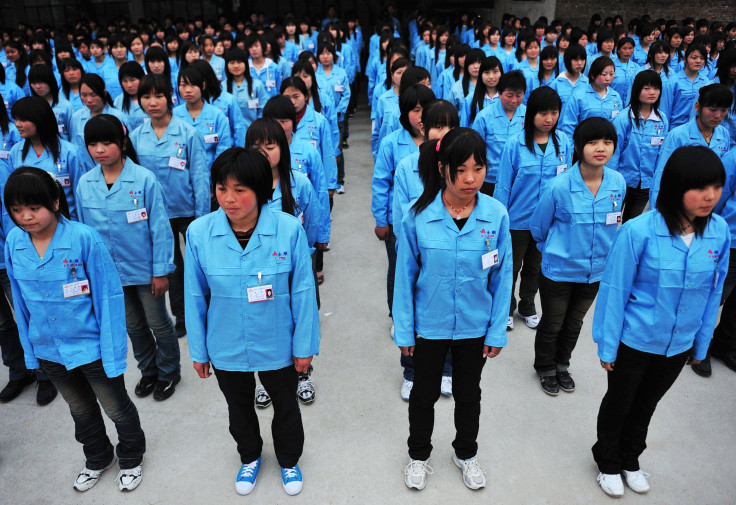
Job Creation
Shenzhen is still, in absolute terms, a flourishing hub of industry and job creation. It’s not surprising, in a city that has budgeted billions of dollars for moving into high-tech sectors. At Shenzhen’s recent high-tech fair, an entire hall was devoted to the city’s drone production industry. Great emphasis is also being placed on areas such as cloud computing and robotics. Financial services, including insurance and business related to the city’s stock market, are growing too. And real estate is also still booming here: though new construction is down, as everywhere in China over the past two years, house prices in Shenzhen have risen more than 30 percent in the past 12 months alone, outpacing any other Chinese city.
Yet many of these new sectors are less labor-intensive than those that are shedding workers.
A few big companies are still hiring. At the bus stations in industrial Shenzhen suburbs like Longhua, big companies such as local telecom giant ZTE, and Foxconn, the Taiwanese supplier of Apple’s iPhone, still put out calls for migrant workers from the hinterland, fresh off the bus, to take production line jobs. But migrants who lose factory jobs are more likely these days to find opportunities in the service sector. Across Shenzhen, many shops and restaurants have signs in their windows saying that they’re hiring staff.
In a sense, this is part of the plan of Shenzhen and other parts of Guangdong, which, some eight years ago, made a conscious decision to gradually phase out low-level, often polluting industries, and bring in less labor-intensive high-tech industry and create more service jobs.
But economists say the wages in the types of service jobs currently available in Shenzhen are often lower than what migrants would earn in factories. The starting salary for many sales jobs in stores in downtown Shenzhen is 2,000-2500 yuan, or around $300 – 400. On average, that’s some $100 - 150 dollars lower than the starting wage for most factory jobs. According to Julia Wang, Greater China Economist at HSBC, such jobs tend to create less economic value too:
“People in the cities [who] are laid off… may find a service job,” she says, “but in terms of the value that a worker produces, services is only around 80 percent as productive as the manufacturing sector. If you take financial services out of the picture, it’s even lower,” she adds. “So while there’s robust growth in the service sector, it’s insufficient to offset the dramatic slowdown in manufacturing.” Wang also notes that, other than financial services, “the growth rate of the service sector is still slowing too – it’s just that it’s slowing from a higher base.” This is backed up by the data: The rate of job creation in China’s service sector in November was the second-lowest monthly figure in 18 months — and overall “factories shed more workers than service providers could hire,” according to the latest Caixin PMI survey.
Lower Wages
Reduced wages mean less purchasing power for those involved – which could have a knock-on effect on government attempts to stimulate consumption. Luo Yingdi certainly knows the feeling: These days the migrant worker from rural Guizhou province in southwest China spends her afternoons and evenings cleaning and setting tables in a restaurant in Longgang, one of Shenzhen’s less affluent suburbs – for a wage of little more than 2,000 yuan (some $300). But until two months ago she was earning more than double that, assembling smartphone components in the nearby factory of Fosunny Electronics. It seemed like a job with long-term prospects: Fosunny was one of the longest-established suppliers to China’s telecoms industry, which has boomed in recent years; it had supplied international customers including Vodafone and AT&T, as well as major Chinese smartphone brands like Huawei and ZTE.
But two months ago, at the end of China’s National Day holiday, Fosunny’s workers suddenly found themselves out of a job.
“I still don’t know why the factory shut,” says Luo, with a shake of her head. “First they gave us a few days off for the holiday, then they told us not to come back for a few more days, saying they were renovating the factory – and then we heard they were laying everyone off.”
The sudden shutdown – which the company blamed on cash-flow problems, a growing problem in China’s economy this year — led to protests by workers at the district government offices. Luo herself says she was lucky – she got a pay-off based on a year’s salary, and she was able to find a job in the restaurant where her husband works as a security guard. But the lower wages are hardly ideal. The couple have to pay rent on their nearby room, in a city where rents are rising fast, and as migrants they are not entitled to send their 6-year-old daughter to a free state school so must pay for her to attend a small school set up by other migrants nearby. And Luo doesn’t like the work so much either:
“I’m not used to this,” she says. “It’s more tiring. In the factory you’re just sitting down, you don’t have to walk around all the time – and you can chat to people. If I could find another factory to work in, that would definitely suit me better.”
And some migrants have been even harder-hit by signs of a manufacturing downturn:
“There’s nothing for me here today,” says Xiao Hong dejectedly, as he scours the job advertisements at one of Shenzhen’s official labor exchanges. The Guangdong native in his early 30s has been out of work for three months, since being laid off by a factory that made Bluetooth headphones. He’d worked there for four years, and had moved up to the sales department. “I was doing very well,” he says. “But recently their business wasn’t so good, so they laid some people off. And the first people they laid off were the ones with skills, whose salaries were higher.”
Xiao, who comes from another part of the province, says he wants to stay in Shenzhen and set up his own e-commerce business, but he doesn’t have the resources. For now, he’s looking for another job, but so far his visits to employment agencies have brought only disappointment. “I can’t find a job where I can use my skills,” he says. “I’m looking for a job with a high-tech company, but the economy’s not so good, and I can’t find anyone hiring.”
Xiao is feeling the pressure. His rent is more than $200 a month for a single room, and he’s worried about paying it. He’s already had to cancel his mobile phone subscription. He may just have to lower his sights, he says – though the prospect doesn’t exactly inspire him. “I’m not in a good mood today,” he says apologetically, before repeating, like a mantra, “I have these skills, but can’t find a job to use them.”
The lack of better-paying jobs undermines not only workers’ ability to spend but also the social equality that many experts say China needs to create a more equitable society and one with sufficient domestic demand to compensate for slowing exports. Guangdong’s economy has already shown some signs of pressure — while it is still growing faster than China’s national average, last year it missed its growth target. That GDP growth of 7.8 percent was the province’s lowest level in 25 years, since the early days of China’s economic reform, according to research by the Economist Intelligence Unit – which predicts the figure will drop to 7.7 percent this year.
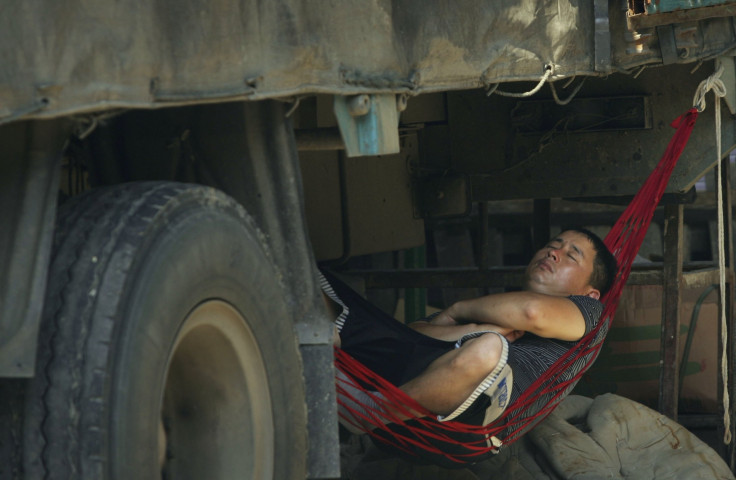
Silver Lining for Manufacturers?
A tightening labor market could be expected to have one beneficial result for Chinese business owners, analysts say: helping to stem the rise in costs that has made life harder for many Chinese manufacturers. Labor costs in wealthier parts of China, adjusted for productivity, are now higher than those of Taiwan or Russia, according to a recent survey by Boston Consulting. Demographic changes have played a part: China’s one-child policy has meant that in recent years there have been significantly fewer young workers coming onto the labor market each year than did a decade ago. And the younger rural migrants tend to be better-educated, better-informed, and less willing to take low-paying production line jobs. All that has added to the pressure on manufacturers like packaging company owner Grace Zhang.
“Ten years ago, our skilled workers got 500 yuan a month. It was very low,” Zhang says, “Now they start at 3000. It’s gone up six times in a decade – imagine that! Now there’s a government-set minimum-wage level – and it’s going up every year. And rent has gone up a lot too. Everything has gone up.”
This year, Zhang says, she has had more people calling her looking for work, not that she has any to offer. It also seems that workers are now more likely to stay in their posts, according to Liu Kaiming, a specialist on migrant workers who runs a Shenzhen NGO called the Institute for Contemporary Observation. In contrast to recent years, he says, migrants in Shenzhen can no longer rely on changing jobs regularly to get a better salary.
Service Before Production
Nevertheless, Liu says factory salaries in Shenzhen have not fallen this year, though there have been slight falls in some inland Chinese provinces, where fewer jobs are available. One reason for this is the tendency among young migrants to forgo production line work in favor of a service job, even if it means lower wages.
“The young want better jobs these days,” Liu explains. “For them it’s not just about money. They might actually earn less in a service job – but they want to do something more interesting.”
Until this year, some factories in Shenzhen and other parts of Guangdong were actually complaining about labor shortages; a few even resorted to employing illegal immigrants, smuggled in from Vietnam by human traffickers, to work for lower wages, according to Chinese media reports.
Lucy Xu, a migrant from Hunan province in her early 20s, who works in a labor agency for newly arrived migrant workers at one of Shenzhen’s long-distance bus stations, explains how many young people think:
“A lot of people don’t want to work in factories; they feel too depressed,” she says. “In the factory, you’re like a machine. Lots of people can’t stand it. We prefer to be more free.”
If they do have to work in factories, Xu says, some young people these days would prefer to stay in their home areas inland, where some factories are moving to reduce costs. They can be nearer their families and children -- tens of millions of whom have been left behind at home by Chinese migrant workers – and also save the significant sums of money they have to spend on rent and living in a relatively expensive place like Shenzhen. At the same bus station, one company is actually touting for workers to leave the city and go to work in Jiangxi, 1,000 miles inland.
Economist Julia Wang of HSBC suggests that a downturn in manufacturing in Shenzhen could actually slow the flow of migrants to the city – which might only push wages up. Wang notes that China’s total number of migrant workers has not increased this year, according to official figures.
“Because the manufacturing sector is so productive, it’s the tide that lifts all boats” she says. “So the slowdown of such a sector would mean that the incentive for migrants to come to the city would slow too.”
Downturn for Dongguan
Other parts of the Pearl River Delta are struggling even more under the combined weight of higher wages, picky workers, and slowing demand. Just half an hour’s train ride up the line from Shenzhen lies Dongguan, where the challenges of trying to move up the value chain are all the more obvious. Dongguan is another of China’s 1990s’ boom towns: Its population grew from less than a million to more than 10 million in little over a decade, as it became one of the world’s biggest manufacturing bases for cheap clothing, shoes and toys.
In recent years, the local government has tried to promote a move away from these core industries, with more electronics and high-tech manufacturing. Yet while wages here are on average only two-thirds of those in Shenzhen, the city has seen challenges: Microsoft recently closed a Nokia factory here, to move it to Vietnam.

Source: National Bureau of Statistics of China
David Zhuang, the Taiwanese boss at Ruida, a clothing factory in Dongguan, has experienced much of the process firsthand. He moved here from Taiwan in the 1990s to take advantage of labor costs that were lower than those back home. But recently it's harder for him to find young people willing to come to the factory to learn a trade; most of his staff are now in their 30s or 40s, and salaries have risen sharply. And in the past few years, more and more of the orders his company used to get for T-shirts and other basic garments have been going to countries like Cambodia and Bangladesh, where labor is much cheaper. Some of his fellow Taiwanese manufacturers have moved their factories there too.
As a result, Zhuang’s company now employs only 50 workers, compared to 200 at its peak. And this year he’s seen the company’s staple business – orders for high-end garments from major European retailers – fall by 50 percent. “Every year we think it’s going to get better next year – but so far it hasn’t happened,” he says. With the continuing high tariffs imposed on Chinese-made goods by many countries, and rising costs, he and his fellow investors are debating just how much longer they’ll continue operating their own production base in China.
In part, Dongguan’s textile industry has fallen victim to the city’s attempts to move up the value chain. Garment factories, particularly those making jeans, have been responsible for serious pollution, and the authorities resolved to clean up the sector. Zhuang says his company has complied with considerably tighter new environmental standards, but has received little encouragement to develop further.
“It’s been very hard for us to get loans to buy the machines we need to upgrade our production,” he says. “Now no one wants to invest in this industry here. Yet our industry gave a chance to lots of people who later set up their own companies – that’s not so easy with electronics,” he adds.
Zhuang laments the lack of long-term vision among many of the area’s entrepreneurs, which he said has hindered the building of brands strong enough to endure. “Some people who ran companies just wanted to maximize profits – so they moved to another part of the country, or they closed their factory and invested in real estate.”
The failure to build up Chinese brands has hit his own business, too, he says. Orders from Chinese clients have fallen because they’ve struggled to build brands to compete with the big-name Western high-street brands, like H&M and Zara, that have entered the Chinese market in recent years.
And without as much of a middle class as Shenzhen to sustain its service industries, Dongguan has been hard-hit by the flight of factories — and workers. A supplier to a major electronics brand, located just behind Zhuang’s own factory, suddenly closed down earlier this year. Real estate prices have fallen in the area, he says, and property is not selling as fast as it used to. An increasing number of shuttered stores with “To lease” signs on their doors now line the streets of Changping district, the center of the city’s textile industry. The queues in the restaurants are getting shorter as well, Zhuang says.

Moving Up the Value Chain
HSBC’s Julia Wang says these problems may be an example of the risks inherent in China’s attempts to move up the value chain in a hurry.
“There’s been a lot of talk about rebalancing in China,” she says. “But we tend to feel that at this point in time, the kind of rebalancing we had may have been a bit too premature. Of course, China does have polluting sectors that may become out of date and should be eliminated in fair competition, but that’s not really a good argument why we should get rid of the manufacturing sector altogether,” she adds. “Other parts of the sector can learn from frontier economies, and move up and grow their technology. We are of the view that to escape the middle-income trap, China actually probably needs to stay on the manufacturing route a little bit longer, because it’s very productive.”
Dongguan’s problems are a microcosm of those in other parts of inland China, where the service industry is far less developed than Shenzhen, says labor expert Liu Kaiming. Certainly some workers in Dongguan are voting with their feet – and heading for Shenzhen itself.
At a local bus station, Liu Jun, a migrant from Jiangxi province, is on his way to Shenzhen with two friends, in search of a higher income. He has worked in an electronics factory in Dongguan for five years, he says, starting out as an ordinary worker and moving up to production management. “But the salaries are not so ideal here – not as high as in Shenzhen,” he says. “And I didn’t feel like the prospects were very good, so we’ve quit our jobs and now we’re going to Shenzhen to look for something better.”
Others are still arriving in the region for the first time. At Shenzhen’s Longhua bus station, 18-year-old Zhou Yi has just arrived from Guangxi province. He’s just graduated from vocational college and wants to find a job in an electronics factory. "The wages are so low back home. I want to come here, get a job, and learn new skills,” he says. “I know there are much better opportunities in Shenzhen. I can earn more, and save enough to send money back home to my family.”
For the moment, Zhou may fulfill his Shenzhen dream. An agent has arranged an interview for him with one of the city’s big electronics factories. But just how much he’ll be able to earn in the city, and whether he’ll get the chance to contribute to the upgrading of the city’s industrial structure is uncertain -- like the city itself, Zhou is taking a big step into the unknown.
© Copyright IBTimes 2025. All rights reserved.