Robots Coming to Aircraft Assembly to Cut Cost
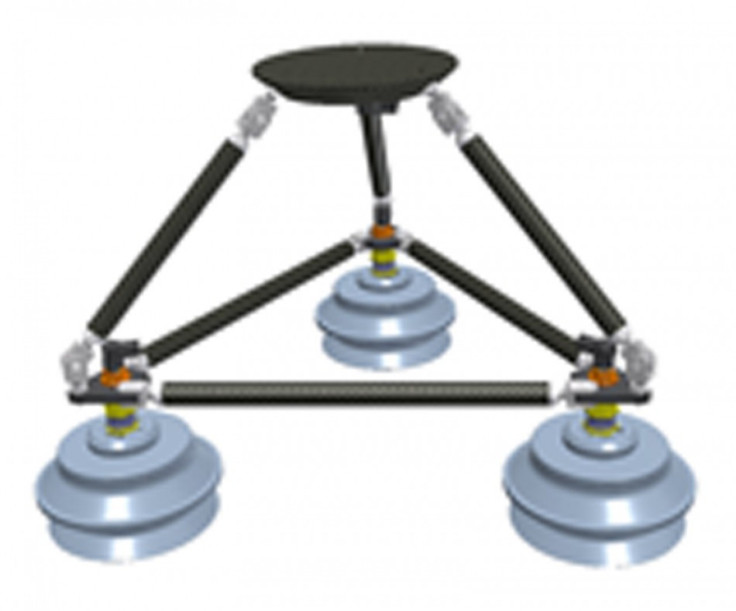
Fraunhofer researchers have created a flexible assembly-line concept for aircraft that features robots working in the same way they do in automotive production.
The giant parts of an aircraft and individual fuselage segments can measure ten meters or more. Therefore, they need to be fitted together with much precision. Aircraft manufacturers can only tolerate a 0.2 millimeters maximum deviation from - on components that weigh several metric tons, researchers say.
And, in order to accurately position these enormous parts, manufacturers depend on massive production facilities known as assembly cells. These are huge gantries moving along the fuselage like container cranes on steel rails and massive concrete foundations. They perform works such as bolting aluminum parts together.
To build these necessary facilities is expensive and time-consuming. It also takes a lot of money and effort to build these kinds of assembly cell. Moreover, these calls need to be built from scratch for each new kind of aircraft, which pushes production and construction costs even higher, researchers say.
This, researchers say, is the reason why the process of aircraft assembly must be automated. They believe it will make high-precision drilling, milling and adhesive bonding simpler, more flexible and more economical in the future.
Developers at the Fraunhofer Project Group Joining and Assembly FFM at the Fraunhofer Institute for Manufacturing Technology and Advanced Materials IFAM, Bremen, are working on such technology.
The developers will present their new manufacturing approach at the Composites Europe trade fair in Stuttgart, Germany, where one of the future assembly line's first elements will be showcased. It's a versatile component gripper made of lightweight CFRP (carbon fiber reinforced plastic).
The fair is being held from Sept. 27 to 29.
Aircraft are made up of shells of varying curvatures, and a gripper system has to be able to adjust accordingly, says Dr. Dirk Niermann, head of the Fraunhofer FFM.
Niermann and his team of developers were the ones to come up with a design they believe is a suitable facility to replace the common assembly cell.
They envision fuselage segments, tail fin and wings sitting on top of a kind of rolling assembly line and being carried past one-armed robots. These robots will then work at various points on the parts in succession to bond, drill and mill them as they pass.
Facility of this kind would still need to be tailored to each new aircraft type, but the installation costs acquired would be significantly lower, researchers say.
No longer will the aircraft parts have to be compressed or bent slightly in order not to breach the overall 0.2 millimeter tolerance.
That's why we're developing a high-precision recognition system to measure the components exactly during assembly, Niermann says.
© Copyright IBTimes 2024. All rights reserved.