Industrial Robots Could Be 16% Less Costly To Employ Than People By 2025
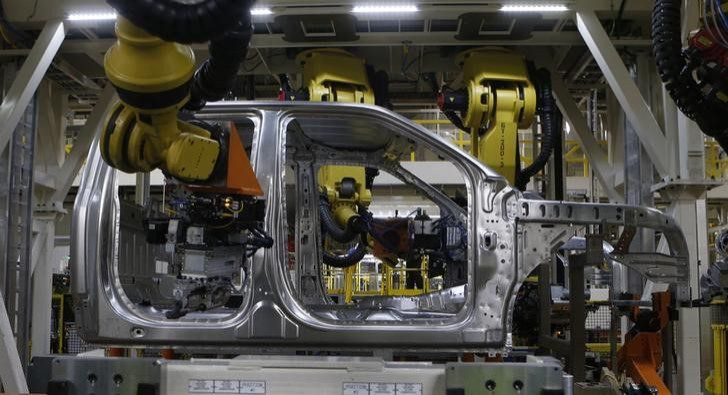
Humans of Earth, beware. Silicon Valley computer engineer and author Martin Ford has a warning: Global income inequality and unemployment will worsen as machines become increasingly capable of replacing human labor at a lower price. That's the message of his book, due out in May, called “The Rise of the Robots.” Meanwhile, a new report puts some numbers behind the use of industrial robots over the next decade.
“For many manufacturers, the biggest reasons for not replacing workers with robots have been pure economics and technical limitations,” Michael Zinser, a manufacturing expert at The Boston Consulting Group (BCG), said in announcing research released Tuesday by the global management consulting firm. “But the price and performance of automation are improving rapidly.”
BCG found that global industrial robots sales leaped 23 percent last year, and deliveries could double to 400,000 a year by 2018.
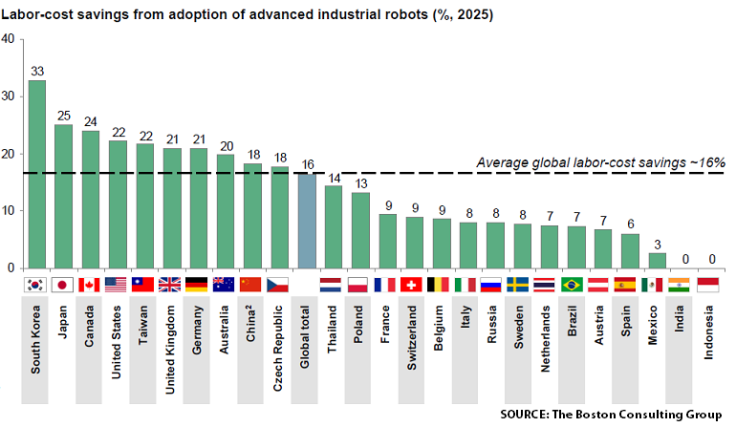
The report estimates that a decade from now the global average labor-cost savings of replacing people with robots will be 16 percent, thanks to the lower costs of manufacturing the mechanical manufacturers. Companies like Boston-based Rethink Robotics are already offering agile factory robots for as little as $25,000, which is equivalent to paying a full-time human worker $4 an hour over the lifetime of the machine, according to a Stanford University study. That’s a price low enough to lure smaller manufacturers.
The average spot-welding robot used in the manufacture of durable goods like cars has dropped from $182,000 in 2005 to $133,000 last year, according to BCG. Costs of industrial robots will continue to decline over the next decade by more than 20 percent. Industrial robots in U.S. auto manufacturing are already operating at a cost roughly matching a typical U.S. fast-food line cook’s wages (barely over the federal $7.25 hourly minimum wage) after the cost of the robot is recovered. Robots used in electronics manufacturing cost less than half of that minimum wage, and that gap is expected to widen -- in the machine’s favor.
BCG says the highest cost savings of using robots in manufacturing will be in advanced economies, like South Korea and the United States, where manufacturing labor costs are highest. But even businesses in emerging markets where labor costs are lower, such as Mexico and Thailand, are expected to see robotics labor costs lower than human sweat by 2025. While this bodes well for manufacturing employers, the employees (the human ones) will face fewer job prospects. And what jobs will be available to them will require more than the rote, low-skill manufacturing-labor activities many emerging markets depend on to create jobs.
Robot adoption varies by country, with China, the United States, South Korea, Germany and Japan currently buying up 80 percent of industrial robots. The fastest rate of adoption is occurring in East Asia, led by South Korea, Taiwan and Thailand.
Three-fourths of advance robot installations is occurring in the manufacturing of transportation equipment, electronics, electrical equipment and machinery.
For a summary of the report’s findings click here.
© Copyright IBTimes 2024. All rights reserved.