At Lear Corporation (LEA), And Elsewhere, Southern Manufacturers Grapple With Increasing Labor Agitation
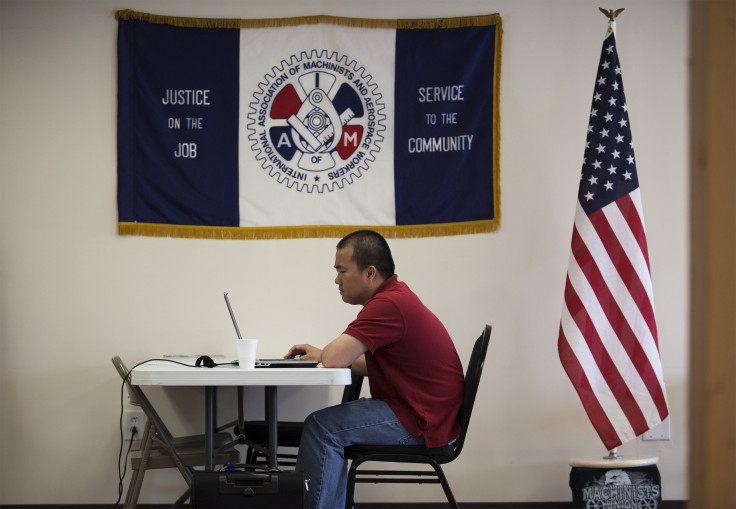
By choosing South Carolina to host its first auto factory in the United States, Volvo followed a trend set by dozens of other manufacturers before it: setting up shop in the American South, where labor costs are relatively low and the threat of unions is diminished.
However, recent agitation in Southern manufacturing casts doubt on the notion that newly arrived employers can take labor peace for granted.
Alfonzia Richardson, 46, makes $14 an hour in the materials department of a Lear Corp.-owned auto parts supplier in Brookwood, Alabama. The factory opened last summer to service a nearby Mercedes-Benz assembly plant outside of Tuscaloosa. Last month, Richardson and his co-workers publicly announced their intent to form a union.
“I want to earn a livable income to support me and my family,” says Richardson, a widower with a 9-year-old daughter. Wages, Richardson points out, are higher at Lear plants represented by the United Autoworkers (UAW) union, which range from $16.50 to $21.58.
Employees also want a raise at another Lear-owned parts supplier in Alabama -- a factory in Selma that makes foam seat cushions for the nearby Hyundai plant. Letasha Irby, 36, a production line worker who supports two young children on her $12 hourly wage, says she feels like a union is “the only way to get positive change.” “Without a contract,” she says, the company “can go back on their word at any time.”
Richardson and Irby are joining hundreds of others outside Lear’s annual shareholder meeting in suburban Detroit on Thursday, calling for improved wages and working conditions. Most of the company’s U.S. factories are unionized -- but not its two sites in Alabama or another one in South Carolina, which, together, supply some of the region’s big auto assembly plants. As those larger plants moved below the Mason-Dixon Line, Lear followed them.
“We respect the right of all our employees to decide to form a union or not,” says Lear spokesman Mel Stephens. He stresses all three plants pay “competitive wages” for the area.
The company isn’t an exception. In recent years, several other manufacturing companies have faced organizing drives after moving South.
Last November, more than 150 workers at a brand-new, Chinese-owned copper pipe factory, lured to rural Alabama’s deeply impoverished Black Belt by millions in tax breaks, voted to join the United Steelworkers union. The UAW announced earlier this week it is, once again, seeking recognition from Volkswagen to represent 1,500 workers at the company’s six-year-old assembly plant in Chattanooga, Tennessee, about a year after losing a bitterly close election there. Meanwhile, other UAW campaigns roll on at Nissan’s massive assembly plant outside of Jackson, Mississippi, and the Mercedes plant near Tuscaloosa. As does an organizing drive from the International Association of Machinists at Boeing’s sprawling aerospace plants outside of Charleston, South Carolina.
Michael Randle, owner and publisher of Southern Business Development, isn’t convinced the organizing will amount to unionization.
“I don’t see it happening anytime soon,” says Randle, whose publication has chronicled the arrival and development of auto manufacturing in the South. Auto unions thrive in situations of labor exploitation, unsafe workplaces and in organizations that have a dearth of training options, he says, and “those conditions aren’t as present” today.
Pro-UAW workers disagree.
Pay isn’t the only issue in Selma, according to employee Letasha Irby. Several workers there say they’ve become sick from exposure to a chemical used in the seat-manufacturing process called toluene diisocyanate, or TDI, contracting asthma, shortness of breath and sinus problems. Last year, the Occupational Safety and Health Administration issued Lear a $9,350 citation for failing to provide workers with proper protective equipment. OSHA has since approved air-quality standards at the facility, but critics aren’t content. They say the agency’s existing rules are inadequate.
Whatever grounds there may be to unionize, a number of barriers apply to organizing Southern manufacturing, says Nelson Lichtenstein, a labor history professor at the University of California, Santa Barbara. Wages for jobs in the communities around facilities tend to be relatively low, which, in turn, dulls the appeal of demands to hike pay. Also, managers -- and increasingly local political figures -- have proven adept at stoking cultural hostility toward unions, especially among white male workers.
On top of that, unions themselves tend to invest fewer resources in organizing Southern workers, since the presence of so-called right-to-work laws reduces the overall payoff. These state-level provisions, which make it harder for unions to collect fees from workers they represent, tend to result in fewer dues-paying members and less powerful unions. The UAW is in a different situation compared with other unions, he says, since it’s faced with the “existential” crisis of the auto industry relocating en masse.
Nevertheless, Lichtenstein notes recent union-funded protests by low-wage workers are starting to have an impact by “raising expectations.” Demands for a $15 hourly wage have become mainstream: “This was thought to be a pie-in-the-sky demand by Occupy types, but it’s gotten traction and helped transform conventional wisdom.”
Richardson, for his part, says he hadn’t heard of fast-food organizing before he got in touch with the UAW but says he’s supportive, since “everybody needs a livable wage.” He also rejects the familiar picture of the UAW as an out-of-touch band of intruders from Detroit. “It’s not an outside third party,” he says. “We are the union.”
© Copyright IBTimes 2025. All rights reserved.