US Manufacturers Aim To Reduce Costs By 1.5 Percent In 2013 To Drive Margin Growth
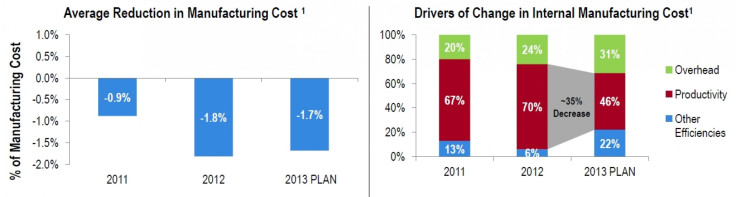
U.S. manufacturers show signs of reshoring as demand stabilizes around the world.
The Hackett Group surveyed 45 manufacturing companies in late 2012 to evaluate how they optimize cost structures and how they choose to invest. Data suggests that companies are targeting an aggressive 1.5 percent reduction in cost of goods sold (COGS). The goal of such a reduction will be to enable margin improvements as organizations increase supply chain investment.
Companies surveyed plan to invest in their supply chains by nearly 3 percent in 2013. Only 20 percent of the total investment will go toward upgrading or building new capacity (down by half from 2012). Investing will instead prioritize IT and training to improve processes, plus supply partners to develop joint capabilities.
"For 2013, companies are clearly focusing on building the skills and infrastructure they need to take advantage of these trending opportunity areas," said Dave Sievers, a principal and the practice leader of The Hackett Group's Strategy & Operations Practice.
Through 2011, companies had still outsourced aggressively to reduce their costs. Then beginning in 2012 many expected far less savings from outsourcing which continues to be the expectation for 2013. This trend is expected to reach a crucial tipping point by 2015 as the total landed cost gap between the U.S. and China continues to shrink. Rising wage inflation in China and continued productivity improvements in the U.S. is driving manufacturers to reshore.
Favorable energy prices were alse key. "With demand really beginning to stabilize in 2012, companies began to optimize their existing distribution networks, reducing overhead and operating costs," said Len Prokopets, associate principal, The Hackett Group's Strategy & Operations Practice. "We expect this to be a significant trend going into 2013."
© Copyright IBTimes 2025. All rights reserved.