General Electric (GE) Talks 3D-Printing Tech: Q&A On Additive Manufacturing
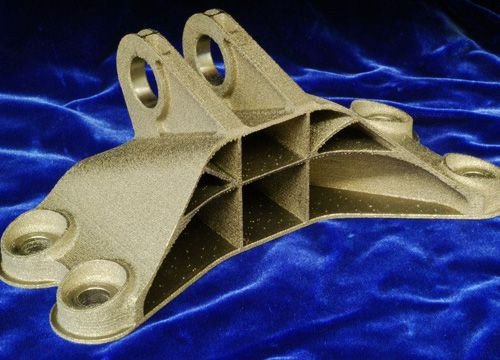
General Electric Company (NYSE:GE) is a proponent of additive manufacturing, a broad category of manufacturing that includes the fashionable and fascinating phenomenon of 3D printing.
Additive manufacturing builds objects by adding parts together in layers, rather than taking raw material and “subtracting” excess material away from fitted molds, as in traditional “subtractive” manufacturing. Additive manufacturing isn't new but was typically used for small plastic prototypes of objects, aiding design tweaks.
But mass production of metallic objects fit for actual industrial use, built up layer-by-layer and modeled through software, has sparked excitement in manufacturing. We spoke to General Electric’s Christine Furstoss, the company’s technology director for manufacturing and materials technologies.
Q: A lot has been written about GE’s 3D-printed fuel nozzle for its aircraft engines. Could you explore other applications of 3D printing or additive manufacturing at General Electric?
A: In Oil & Gas and in Power & Water, initially we’re looking closely at our combustion systems. We invest a lot in that technology because we continuously want to lower emissions and reach higher efficiencies with more-effective uses of fuel and fuel flexibility.
Combustion systems and all their associated systems have very complex pieces. Using additive allows us to try some very novel ways of looking at design. Emissions and fuel-efficiency performance is a large thrust here. This involves multipiece fabrication, small machine parts, and injection molded parts that have to be combined. These are very intricate combinations that had to be welded together, brazed together so we can get more tested faster, and accelerate the design process for new products across turbomachinery and combustion.
For many of our turbomachinery businesses, which captures Aviation, Power & Water, Oil & Gas, we’re using additive technology for repairing and servicing parts, such as gears, structural components, casing and even some aerodynamic blades. (Some turbomachinery helps run the pumps that get oil out the ground.)
We’re very bullish on using additive manufacturing to help service parts in the field. Whether repairing existing parts or building new ones, this opens up new business models on servicing our equipment. We can give spare parts to our customers in a very cost effective and fast way.
Q: What are some obstacles to widespread industrial adoption of 3D printing?
A: Let me list three things that will cause step changes in the adoption of additive 3D printing.
One breakthrough will come when we have better closed loop control. That’s the whole issue around control systems. That’s the heart of automation, which some people view as older technology, but for me that’s the game changer.
Everything must be combined with different sensors or inspectors looking at things that impact the final properties of the part, like how quickly a laser moves, what power it runs at, how thin that surface is, how thick you’re building each layer. That control of properties controls the parameters of the final part to such a high degree. You want to be sure that if things start to drift or get misaligned that the machine senses it and can compensate.
It should be an interesting engineering problem, but one that can be solved. Let’s remember that we’re working with lasers and metals. It’s hard to sense, and these processes are occurring at temperatures well over 2,000 degrees. How do you make sense of these signals, and how do you do it in real time?
Second, we need a better fix on the materials used during additive 3D printing. In the polymer world, there are very good large industrial producers like Stratasys, Ltd.'s. (NASDAQ:SSYS) 3D systems. But their material sets are very unique to their equipment.
How do you identify and qualify such materials when you get into the metals world [not just plastics]? These materials have to flow very easily because we’re ingesting them into machines. You need flow, since you don’t want to clog things up, but in the end you must have properties that can make aircraft engines, so they have to have certain material properties.
Companies that dedicate themselves to materials for 3D printing are just starting to emerge. The more we can learn about the final product and the materials, the more on that relationship, the better. It’s in its infancy. Companies that understand enough about metal powders, and the actual additive process, enough to tailor their material for the process, are only just emerging.
Thirdly, the whole area of inspection. We can print shapes that are so complex and almost unbelievable, but: are all the tolerances met? How do we make sure every surface, every size, and the roughness is where we need it to be?
Q: The U.S. seems to be a leader in 3D-printing technology. Why? Who are some other key players?
A: 3D printing is the ultimate digital meets physical world. It’s the ultimate in using software to virtually design components, then rapidly trying out new concepts and putting them into form. For all the testing we talk about, software is really the heart of 3D printing.
The software used is very important to understanding what additive can do. For instance, you sometimes have to design the part a little differently to compensate for things that’ll happen while manufacturing. The fact is that the U.S. is a leader of software development, and we have the initiative to see the "Brilliant Factory." We’re leading not only because of our heritage in manufacturing but also our prowess in software.
But Germany has many of the machine makers, too, so they have a strong lead. They have a great Fraunhofer institute, which is at a high level roughly equivalent to our National Lab system. They have a tremendous capability in additive.
Q: Some analysts are skeptical of 3D printing beyond the novelty of the technology, predicting that it’ll only impact a small slice of global manufacturing. Does that concern you? Does that matter?
A: It doesn’t matter as long as we continue to have some scale at both the machine and materials level. Besides the machines and materials, there’s also the software production. So there doesn’t need to be massive scale. Even between 5 and 20 percent, and we can debate what that number is -- it could easily be 20 percent -- that’s a nice scale across the world and pretty good volume.
So long as there’s a continuous push for a 3D-printing ecosystem, I think we’ll be fine. But I do contend that additive will touch more of the economy than just the industrial economy. I think the use of additive 3D-printing tech for things like tooling will grow at the most-rapid pace. These are parts that are a little simpler, and more forgiving on the needed material properties, because you’re using them as tools.
A big push for us is making small batches of parts to use in test vehicles. There additive is making an impact. If you look at the number of parts that will be touched by additive, maybe prototyped or made by tools made by additive, the economic impact quickly climbs.
© Copyright IBTimes 2024. All rights reserved.