Muscles For Future Nano-Robots: Cell-Sized Shapeshifting Device Made Using Graphene, Glass
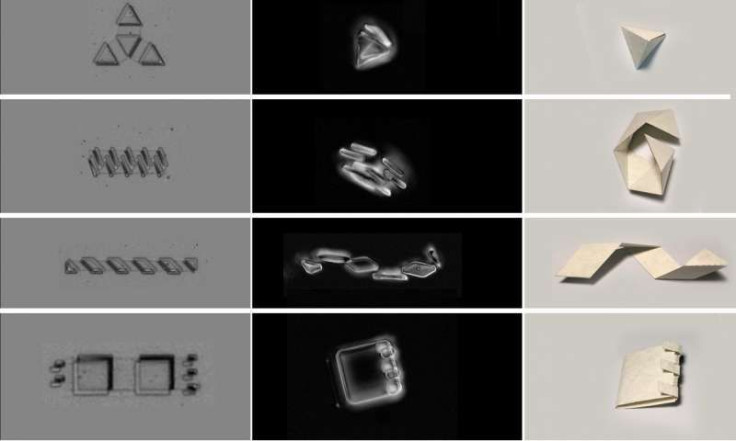
Imagine a robotic cell that can function on its own from carrying electric charge, studying the environment around it and changing shape constantly to adapt to it.
Sounds like something right out of a fictional, futuristic world where robots are built from cells like humans and can do everything we can, but better.
But now, physicists from Cornell University have done just this and given this device microscopic muscles too.
The team has successfully created the world’s first robot exoskeleton that can rapidly change its shape upon sensing chemical or thermal changes in its environment. And, it’s as tiny as a cell. The team has even given it electronic, photonic and chemical properties making it a functioning robotic microorganism.
“You could put the computational power of the spaceship Voyager onto an object the size of a cell,” Itai Cohen, co-author of the study based on the research in a press release. “Then, where do you go explore?”
“We are trying to build what you might call an ‘exoskeleton’ for electronics,” said McEuen, the John A. Newman Professor of Physical Science and director of the Kavli Institute at Cornell for Nanoscale Science.
The only things that come close to this are modern day computer chips. These tiny devices are capable of carrying information and processing it too, but are rigid in structure and fixed to one position.
The machines developed by Cornell scientists move using a device known as a bimorph. A bimorph is obtained when two materials react to external stimulus; the team was inspired by origami to combine graphene and glass to create a bimorph that bends with any stimulus like heat, chemical reactions, voltage or just a prod.
In a bimorph, the two materials react differently to a single stimulus. The change in one of the components of the bimorph puts a strain on the whole structure, which in turn is countered by the other component stretching out to accommodate it.
The team added flat panels on one side of the materials that cannot move. This resulted in a localized rigidity allowing only specific places to move according to the type of stimulus the bimorph received. This led to desirable changes in shape instead of just uncontrolled morphing of layers.
The team used graphene and glass bimorph to make a variety of folding structures ranging from tetrahedrons to cubes, essentially giving it the functionality of a tiny muscle that compresses or expands with stress.
The reason for using a grapheme-glass bimorph is that they also respond to chemical stimuli by driving large ions into the glass, causing it to expand.
The team painted on atomically thin layers of silicon dioxide onto aluminium over a cover slip to give it the rigid layer to facilitate shape changes. Then, an atom thin layer of graphene was put on the stack making the thinnest bimorph ever made.
The team hopes that this discovery will become the future of nano-robotics. The bimorph has the incredible physical properties of graphene-like strength, making it a tiny, durable electronic exoskeleton capable of morphing.
“Our devices are compatible with semiconductor manufacturing,” Cohen said. “That’s what’s making this compatible with our future vision for robotics at this scale.”
“If you want to build this electronics exoskeleton,” he added, “you need it to be able to produce enough force to carry the electronics. Ours does that.”
“Right now, there are no ‘muscles’ for small-scale machines,” he said, “so we’re building the small-scale muscles.”
The study titled “Graphene-based Bimorphs for Micron-sized, Autonomous Origami Machines” was published Jan. 2 in Proceedings of the National Academy of Sciences and was led by postdoctoral researcher Marc Miskin.
© Copyright IBTimes 2025. All rights reserved.