Ways To Increase Production Efficiency
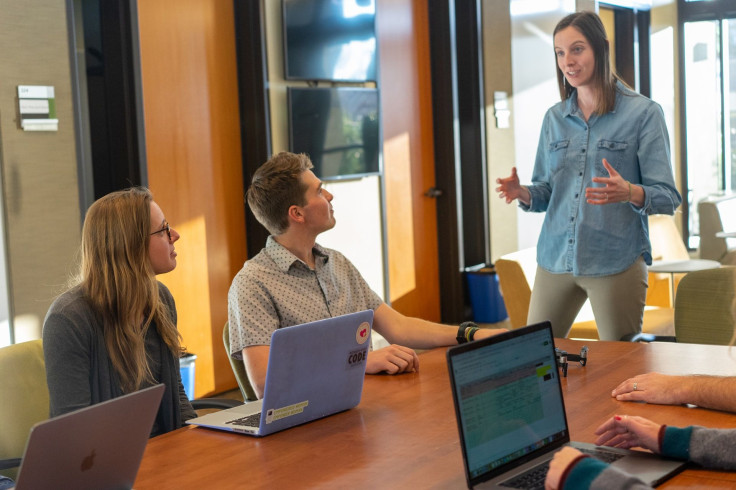
There are no ifs and buts when it comes to production efficiency--it's crucial to every industry. Production's ability to impact labor requirements, costs, outputs, and bottom lines are at levels beyond significant. No wonder companies are always in search of fresh techniques to excel their processes in this department, though its definition can be malleable.
Imagine a firm that views production efficiency as having more projects completed by its production lines. When this happens, employees will likely know it and assume the company's performance indicators and rewards are based on that standard.
But while production output could surge as a result, so might defects and returns. In reality, production efficiency's definition and optimization are unique to your company. But these steps can be a good start for refining the process until you reach your target efficiency rates.
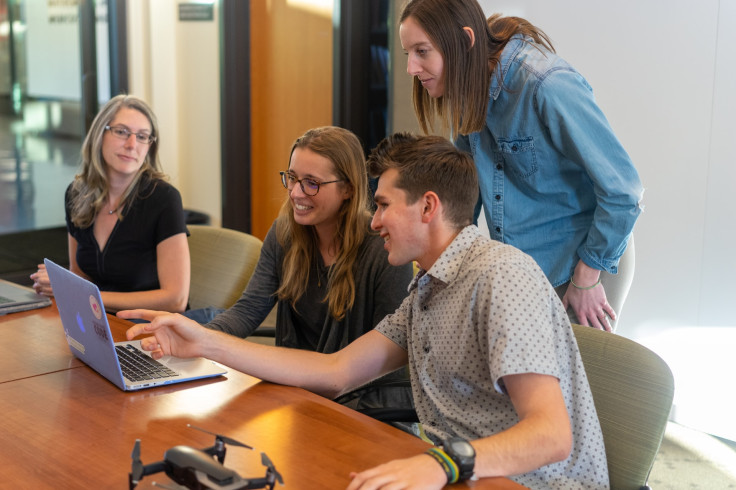
How to Change Your Process to Boost Production
Occasionally, companies upgrade their production equipment and see immediate output gains without considering the technology or resources responsible. They might brag about high-tech machines but still use pen and paper to perform quality control inspections.
This is a clear sign that they're losing efficiency-- they don't understand the potential of their equipment. Let's go over a few ways you can take advantage of that potential.
Assess Production Lines
The production line is among the most vital processes to review and assess when you're trying to improve production efficiency. Start by looking into throughput, or the volume of production per a specific time period. This can bring any issues with your equipment to light.
You should also consider capacity utilization, or the total production output at each production line, using the company's maximum production capacity.
Throughput and capacity utilization not only provide an accurate measurement of a company's production line efficiency, but they also show the impact of equipment downtime. So in a production line with a throughput of $800,000 units per hour, a total downtime of 20 minutes can cost the company around $333,000.
Install New Technology
Unfortunately, technology is a sore point for many businesses. Unless they use the most effective software available, they can't stand a chance against better-equipped rivals. Investments in technology are often hefty, but the reward of rising above competitors can make the cost negligible.
As an example, let's say you have 10 machines, and it takes at least 5 minutes for information to be received at a production line. This could mean over 200 hours of productive time wasted every year. You're practically bleeding money.
Additionally, up-to-date technology increases not only operating efficiency but ]employee morale and retention too. After all, who wants to work with ancient machines?
Untangle Production Choke Points
Production chokepoints are bottlenecks that lead to breakdowns. Obviously, these points are critical to the success of the whole process and you need to identify them as early as possible during routine evaluations.
Managers often assumed that chokepoints are caused by equipment, but in reality, humans are usually behind them. It's true that these problems can happen with the machines, but they're generally avoidable with regular, preventative maintenance. Sometimes, you'll see backups caused by the proverbial red tape. Too many hands in the pot not only increases downtime but also costs.
No matter the cause of a choke point, you should identify and eliminate it before it starts eating into production efficiency. Even if a bottleneck can't be resolved right away, discovering it and working on it at the earliest possible time can make a huge difference to your bottom line over time.
Implement a No-Waste Policy
You can eliminate operational waste in-house, but sometimes, a third party can bring in more solid results. For example, ventilation may feel fine to the people working in a building but only because they're used to it. With third-party experts, they can accurately determine and promptly address inefficiencies. The result? Less energy dependence and costs for your company.
Labor is another resource commonly taken for granted despite its monumental impact on production efficiency. Despite having common goals, employees left to their own devices will likely end up wasting hundreds to thousands of work hours each year.
Smarter use of human physical energy, by setting measurable and workable standard operating procedures, can increase production output without increasing time.
Recycle!
Recycling is a classic cost-cutting method whose benefits are magnified in production lines. Here, you can multiply even the smallest savings to substantial amounts through the entire production process. This makes it worthwhile to sort through leftovers or scraps and throw anything reasonably salvageable back into production.
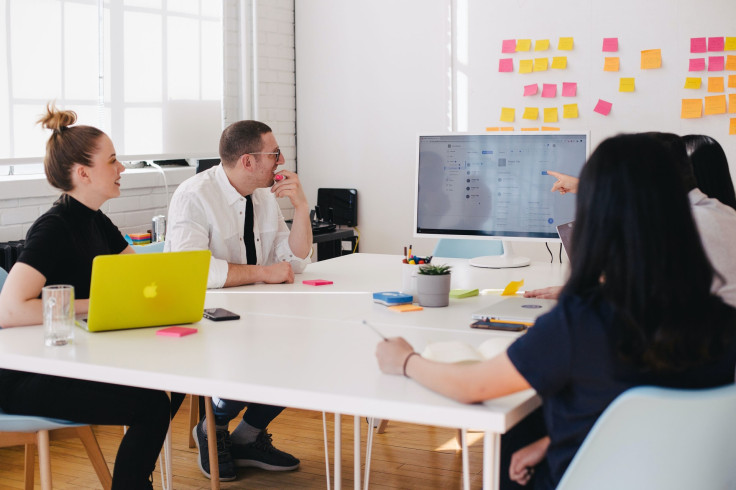
Establish a System
A group that works without a system for execution can never be efficient. So it goes without saying that standardizing processes across the board should be a given. The only way to achieve a decent level of efficiency is with a reproducible system that can be improved over time. It doesn't matter if the task is related to sales and marketing, shipment, or communication.
For example, take a look at how production updates are delivered from the factory to the front office. What set of criteria is used to get items ready for shipment? What communication will you use?
Miscommunication is one of the most common causes of failure in the production process, but there are more. When you establish a system for every aspect of production, efficiency for the entire process automatically increases.
Invest in Skills
It's rare to find an employee who already possesses all the skills you're looking for. In most cases, you'll have to train them in-house so they learn specific abilities and adhere to company standards. As the employer, you should be investing enough resources in quality training.
In the end, all companies aim for the highest volume of production over the least amount of time. If you're scratching your head at current issues in your production processes, these steps can help you increase throughput while maintaining superior product quality.
© Copyright IBTimes 2024. All rights reserved.