The Flexible CNC Machining Model That Makes Rapid Axis Your One-Stop Shop for Any Project Size
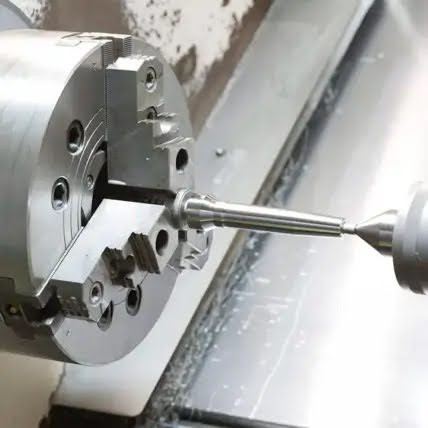
Can quality truly remain consistent when production quantities vary dramatically? This fundamental question strikes at the heart of modern manufacturing, where companies must navigate between prototype runs of single units and mass production demands reaching the millions.
This challenge becomes particularly acute for Computer Numerical Control (CNC) machining, where precision tolerances measured in thousandths of an inch must remain constant whether producing one component or one million.
The California-based custom component manufacturer Rapid Axis has built its reputation on a counterintuitive premise: the same rigorous processes, quality controls, and attention to detail can be applied economically to small-batch prototyping and large-scale production runs. This philosophy challenges the traditional manufacturing paradigm where companies typically specialize in high-volume, low-margin production or low-volume, high-margin custom work.
Rapid Axis serves over [number] regularly purchasing customers for companies of various industries, handling projects that range from single prototype components to multi-million unit annual production requirements. The company's approach represents a departure from industry norms, where manufacturers often compromise quality for speed in small runs or sacrifice flexibility for efficiency in large-scale operations.
Meeting the Demands of Both Worlds: Small Runs and Mass Production
Scaling Without Compromising Standards
Rapid Axis's short-run CNC Machining production capabilities demonstrate how modern machining can maintain precision across varying quantities. Short-run production at Rapid Axis supports specialized products with low annual quantities, delivering components with the same accuracy and speed standards applied to larger orders.
Short-run projects at Rapid Axis could be a single, high-tolerance bracket for a spacecraft, or a low-volume test run for consumer electronics. This range encompasses everything from initial prototypes requiring single units to pilot production runs of hundreds of components.
They are all processed through the same quality management system that earned the company zero findings in its recent ISO 9001 audit. The company's advanced CNC equipment and process flexibility make these projects possible, supported by a highly curated network of partners for additional capabilities.
Tools and schedules are optimized for small quantities, minimizing setup time and cost. This allows customers to obtain components, sometimes in as little as a day, without the burden of traditional tooling or extended lead times.
Rapid Axis's short-run capabilities particularly benefit industries requiring rapid iteration and testing. Aerospace and defense contractors, for instance, often need small quantities of complex components for testing and validation before larger procurement decisions. Additionally, this capability is for companies developing new products, where initial market validation requires small batches before committing to full-scale production.
Rapid Axis's ability to deliver these components with production-quality standards enables clients to make informed decisions about scalability without wondering whether small-batch quality will translate to larger orders.
Mass Production Without Losing Agility
On the other hand, Rapid Axis's CNC Machining mass production services emphasize scale, automation, and strict repeatability. The company can support mass production requirements reaching into the multi-millions annually, utilizing the same comprehensive service portfolio and quality standards that define their smaller projects.
From parts for electric vehicles to precision housings for medical devices, they deliver multi-million unit runs by leveraging the same equipment and core quality controls but introducing batch management and coordinated inspection protocols to handle the volume efficiently.
Proprietary workflow systems, from First-Level inspection, Full First-Article Inspection (FAI) when required, and Advanced Quality Level (AQL) support for production volumes, ensure that even when hundreds of thousands of units move through the facility, each one meets the original engineering intent.
"Obtain your annual, quarterly, or monthly unit requirements with lightning speed, accuracy, and excellent communication for multiple processes through one vetted supplier," founder Jared Probst mentions, emphasizing how its integrated approach eliminates the complexity of managing multiple vendors for large-scale projects.
This single-source capability becomes particularly valuable when tight production schedules and coordination among multiple suppliers could introduce delays or quality inconsistencies.
The Key to Consistency: People
Jared Probst believes that Rapid Axis's consistency among varying project sizes stems from its people, the team of professionals who emphasize systematic design rather than simply scaling existing capabilities. "Manufacturing excellence starts with people. Our team's extensive experience allows them to anticipate potential issues before they arise and implement solutions proactively," Probst adds.
Quality engineers match the requirement with the appropriate type and rigor of inspection: first-article validation for new or complex parts, 100% dimensional checks for prototypes, or robust sampling plans for production runs. All jobs use the same cloud-based tracking and status reporting, ensuring accountability at every stage.
Short-run jobs get direct access to dedicated project managers, who translate evolving drawings and real-time feedback into actionable work orders. These teams work closely with machinists and quality engineers who thrive on challenge, iterating as needed to meet client deadlines or handle last-minute design changes. For mass production, Rapid Axis employs scheduling algorithms and automated processes designed to maximize throughput while minimizing idle time and material waste.
Probst mentions, "Consistency is about expectations and process. It comes from investment in both people and systems, like software, equipment, and partnerships, that can move quickly. We train our teams to look for the details: Are tolerances as specified? Are the finishes correct? Does the part fit its intended use? That's the real challenge and the real opportunity: bring the best practices of both worlds together under one roof."
Approaches Tailored, Standards Unified: The Secret to Flexibility
Serving a customer base that spans aerospace, defense, energy, robotics, and beyond, Rapid Axis recognizes that every project comes with unique constraints, including schedules, regulatory requirements, or sheer technical difficulty. Its "flexible model" is rooted in understanding these needs and engineering workflows that honor them, regardless of order size.
Customers draw confidence from this holistic approach. A prototype order is not treated as a test run to be ironed out in production; every step is subject to the same scrutiny, using production-grade materials and manufacturing conditions. When a design proves successful, scaling up becomes a matter of logistics, not process reengineering.
Probst concludes, "Scale matters, but flexibility matters more. We're here to show clients they never need to sacrifice precision for volume or speed of service. In every unit, the same values apply."
The company's foundation rests on the belief that the barrier between small and large orders can, and should, be flattened by modern technology and a single set of standards mindset.
That is why, whether a project requires CNC machining, sheet metal fabrication, 3D printing, urethane casting, die casting, or injection molding, the same quality standards apply regardless of order size. Rapid Axis stands ready with tools, experience, and confidence that comes from doing the hard work every time.
© Copyright IBTimes 2024. All rights reserved.